To adjust air pressure on an air compressor, locate the pressure regulator knob and turn it clockwise to increase pressure or counterclockwise to decrease pressure. Adjust the pressure slowly and carefully to avoid damaging the equipment.
An air compressor is a vital tool in various industries, providing compressed air for an array of applications. However, it’s crucial to ensure that the air pressure is adjusted correctly to meet specific requirements. By adjusting the air pressure, you can optimize performance, prevent damage to tools, and enhance efficiency.
We will guide you on how to adjust air pressure on an air compressor accurately and safely. Following these steps will equip you with the knowledge to fine-tune the pressure settings according to your needs, enabling you to achieve the desired results effectively. So, let’s dive in and explore the process of adjusting air pressure on an air compressor.
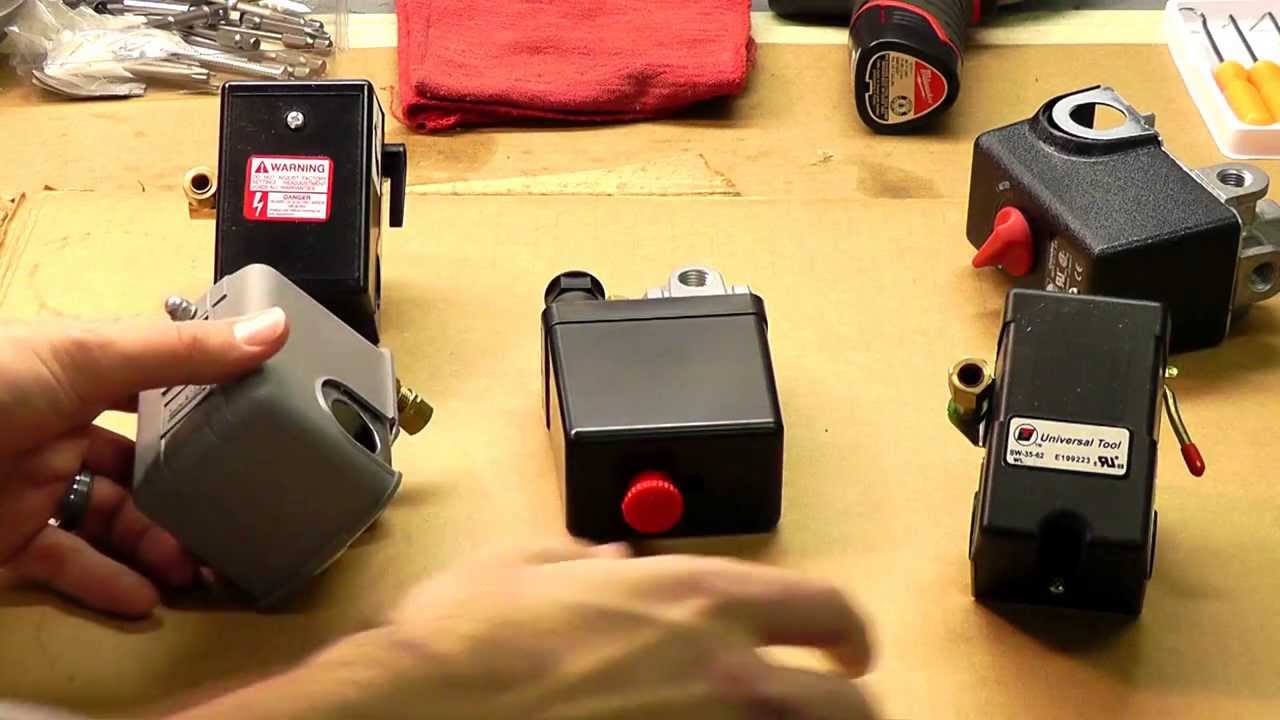
Credit: m.youtube.com
Understanding Air Pressure
Understanding air pressure is crucial when working with an air compressor. Air pressure refers to the force applied by the air within the compressor tank, measured in pounds per square inch (PSI). Adjusting the air pressure to the correct level is vital for the efficient and safe operation of the compressor. In this section, we will discuss what air pressure is and why it is important to adjust it appropriately.
What Is Air Pressure?
Air pressure is the measure of force that air applies to the walls of a container, in this case, the compressor tank. When the compressor is turned on, it compresses the air into a smaller space, which increases the air pressure within the tank. This build-up of pressure allows the compressor to perform various tasks, such as powering pneumatic tools or inflating tires.
Why Is Air Pressure Adjustment Important?
The proper adjustment of air pressure is paramount for the safety and effectiveness of any air compressor. Here are a few reasons why it is crucial to adjust air pressure:
- Efficiency: Adjusting the air pressure to match the requirements of the task at hand ensures optimal performance. For instance, overinflating a tire can lead to uneven wear and reduced fuel efficiency, while underinflating it can affect the vehicle’s handling.
- User Safety: Different tools and equipment have specific air pressure requirements. Using the correct pressure minimizes the risk of accidents and malfunctions, such as tool jams or bursting air hoses.
- Tool Longevity: Consistently using incorrect air pressure can cause excessive wear and tear on pneumatic tools, reducing their lifespan. Adjusting the pressure to the recommended level helps maximize the longevity of these tools.
- Energy Consumption: Running an air compressor at higher pressure levels than necessary can result in increased energy consumption. Adjusting the air pressure to the proper level helps conserve energy and reduces operating costs.
By understanding what air pressure is and why it is important to adjust it appropriately, you can ensure the efficient and safe operation of your air compressor. In the next section, we will delve into the step-by-step process of adjusting the air pressure on an air compressor.

Credit: fluidairedynamics.com
Tools And Equipment For Air Pressure Adjustment
Adjusting the air pressure on your air compressor is essential for ensuring optimal performance and efficiency. To make this adjustment, you’ll need a few tools and equipment. Let’s take a closer look at the types of air compressors, pressure gauges and regulators, and additional tools you’ll need for adjusting the air pressure.
Types Of Air Compressors
There are several types of air compressors available, each with its own unique features and applications. The most common types of air compressors are:
- Piston compressors: Also known as reciprocating compressors, they use pistons to compress the air.
- Rotary screw compressors: These compressors use two rotating screws to compress the air.
- Centrifugal compressors: Ideal for large-scale applications, these compressors use centrifugal force to compress the air.
Pressure Gauges And Regulators
Pressure gauges and regulators are essential tools for monitoring and adjusting the air pressure. The pressure gauge allows you to see the current pressure reading, while the regulator enables you to control and adjust the pressure.
When using a pressure gauge, ensure it is compatible with your air compressor and has an appropriate pressure range. The regulator should also be of high quality to ensure accurate adjustments.
Additional Tools For Adjustment
In addition to pressure gauges and regulators, there are a few other tools that can aid in air pressure adjustment:
- Air hose: A flexible hose that connects the air compressor to the tools or equipment.
- Teflon tape: Used for sealing air connections to prevent leaks.
- Air blow gun: Helps to clean and remove debris from the air compressor and tools.
- Wrench: Used to tighten or loosen fittings and connections.
By having these additional tools on hand, you’ll be well-equipped to adjust the air pressure on your air compressor effectively. Remember, proper adjustments can enhance the performance and extend the lifespan of your compressor, so it’s worth investing in the right tools.
Step-by-step Process For Air Pressure Adjustment
Adjusting the air pressure on your air compressor is an essential skill for anyone working with pneumatic tools or equipment. Incorrect air pressure can impact the performance and efficiency of your tools, compromising your work. In this step-by-step guide, we will walk you through the process of adjusting the air pressure on your compressor to ensure optimal performance and safety.
1. Checking The Manufacturer’s Recommendations
Before making any adjustments, it is crucial to consult the manufacturer’s recommendations for your specific air compressor model. This information can usually be found in the user manual or on the manufacturer’s website. Pay close attention to the suggested pressure range and any specific instructions provided. This will ensure you stay within the recommended limits and avoid potential damage to your compressor or tools.
2. Preparation And Safety Measures
Prior to adjusting the air pressure, take safety precautions to protect yourself and others. Ensure the compressor is turned off, and unplug it from the power source. Release any remaining air pressure from the tank by opening the drain valve. It is also advisable to wear protective eyewear and gloves to avoid injury. Take a moment to inspect the compressor for any signs of damage or leaks.
3. Adjusting The Pressure Settings
Locate the pressure adjustment knob or regulator on your air compressor. This is typically found near the tank or on the control panel. Use the appropriate tool, such as a screwdriver or knob, to adjust the pressure settings. Turn the knob clockwise to increase the pressure or counterclockwise to decrease it. Make small adjustments and monitor the pressure gauge as you go.
4. Testing And Validating The Adjustment
After making the necessary pressure adjustments, it is time to test the compressor. Plug it back into the power source and turn it on. Allow the compressor to build up the air pressure until it reaches the desired setting. Use a pressure gauge or monitor to verify that the pressure matches your intended adjustment. If necessary, repeat the adjustment process until the desired pressure is achieved.
5. Fine-tuning The Air Pressure
Once you have validated the adjustment, it is important to fine-tune the air pressure to optimize tool performance. Connect the pneumatic tool or equipment to the compressor and operate it. Observe the tool’s performance and make any further adjustments to the pressure settings as needed. Fine-tuning allows you to achieve the ideal pressure for a particular task, ensuring efficient and precise operation. Repeat the testing and fine-tuning process until you are satisfied with the tool’s performance.

Credit: www.amazon.com
Frequently Asked Questions On How To Adjust Air Pressure On Air Compressor
How Do You Adjust Air Pressure On An Air Compressor?
To adjust the air pressure on an air compressor, start by identifying the pressure regulator knob. Turn it clockwise to increase the pressure or counterclockwise to decrease it. Use a pressure gauge to monitor the pressure and make small adjustments as needed until you reach the desired level.
Why Is It Important To Adjust The Air Pressure On An Air Compressor?
Adjusting the air pressure on an air compressor is important for several reasons. It allows you to customize the air pressure to suit different applications, preventing damage to sensitive tools or equipment. It also ensures optimal performance and efficiency while minimizing safety risks associated with over or underinflated equipment.
What Are The Common Problems Caused By Incorrect Air Pressure On An Air Compressor?
Using an air compressor with incorrect air pressure can lead to various issues. Insufficient pressure may result in underpowered tools, slow performance, or inability to complete tasks. On the other hand, excessive pressure can cause tool damage, leaks, and safety hazards.
Adjusting the air pressure appropriately is crucial for avoiding these problems and ensuring smooth operation.
Conclusion
Adjusting air pressure on an air compressor is a crucial skill for ensuring optimal performance. By following the step-by-step guide provided, you can easily adjust the air pressure to meet the requirements of your specific task. Remember, maintaining the right air pressure not only extends the lifespan of your compressor but also enables efficient and effective operation.
So, take the time to familiarize yourself with the process and make the necessary adjustments for a smoother and more reliable air compressor experience.